Wer in der Automobilindustrie seine Produkte verkaufen will, kommt nicht daran vorbei, das Analyse-Tool FMEA für seine Fehler- und Risikoanalyse zu nutzen. Und auch Unternehmen aus anderen Industriebereichen setzen auf die FMEA.
Das hat gute Gründe: Die FMEA als umfangreiche Analyse von Fehlermöglichkeiten und den daraus entstehenden Risiken ist eines der ersten Dokumente, die herangezogen werden, wenn es um Produkthaftungsfälle geht. In einem solchen Produkthaftungsfall gilt nämlich nicht „im Zweifel für den Angeklagten“; sondern hier liegt die Beweislast bei dem Unternehmen, das Produkte auf den Markt bringt. Es muss nachweisen können, dass es alles nach bestem Wissen und Gewissen als auch nach zum Zeitpunkt der Entwicklung neusten Stand der Technik alles Mögliche unternommen hat, fehlerfreie Produkte zu liefern.
In der Fehleranalyse müssen alle Fehler die möglicherweise auftreten könnten – so wie ihre Folgen und Ursachen – transparent und so vollständig wie möglich offengelegt werden. Wichtig dabei ist das Mindset: Egal ob ein Fehler schon einmal vorgekommen ist und egal wie wahrscheinlich der Fehler auftritt; der potenzielle Fehler muss dokumentiert werden. Im nächsten Schritt (in der Risikoanalyse) wird dann bestimmt, wie hoch das Auftreten der Ursache des Fehlers ist, wie gut der Fehler (wenn er dann doch einmal vorkommt) entdeckt wird, und wie schwer bzw. bedeutend die Folgen des Fehlers sind. Die drei Bewertungen (Bedeutung der Fehlerfolge / Auftreten der Fehlerursache / Entdeckung des Fehlers („Fehlerart“)) ergeben dann die sogenannte Aufgabenpriorität. Der Name sagt es schon: Die Aufgabenpriorität (eingeteilt in hoch, mittel und niedrig) gibt an, um welche Fehlerarten und Fehlerursachen man sich als erstes kümmern sollte wenn es um die Optimierung von Produkten oder Produktionsprozessen geht.
Die FMEAs (Design-FMEA und Prozess-FMEA) sollten rechtzeitig erarbeitet werden, so dass man – wenn erforderlich – mit konstruktiven Änderungen bzw. Änderungen in der Produktion die möglichen Fehler und ihre Ursachen vorbeugen kann. Je später man seine Produkte oder Produktionsprozesse optimiert, desto teurer und aufwändiger wird es. Wenn Fehler erst beim Kunden oder Endkunden entdeckt werden, kann es zusätzlich noch zum Imageverlust kommen.
So viel zur Theorie.
In der Praxis sieht es anders aus: Oftmals wird von einem Konstrukteur die Design-FMEA bzw. von einem Prozessentwickler die Prozess-FMEA „so nebenbei“ gemacht.
Der FMEA Verantwortliche ist in solch einem Fall oft in ebenfalls wichtige Aufgaben eingebunden (Aufgaben, die im Gegensatz zu der FMEA meist [bis zu einem gewissen Zeitpunkt] dringlicher sind; und oftmals unvorhergesehen sind). Es ist klar, dass dann die Güte und der Nutzen der FMEA nicht besonders gut sind. Hinzu kommt noch, dass ein FMEA Verantwortlicher, der nur wenige Stunden in der Woche bzw. im Monat tatsächlich mit FMEA-Arbeit und -Moderation beschäftigt ist, sich nur bedingt Methodenwissen und Softwarekenntnis aneignen kann.
Autor: Jan Schumacher
Analyse potenzieller Fehler und dem daraus folgenden Risiko mit dem Analyse-Tool FMEA
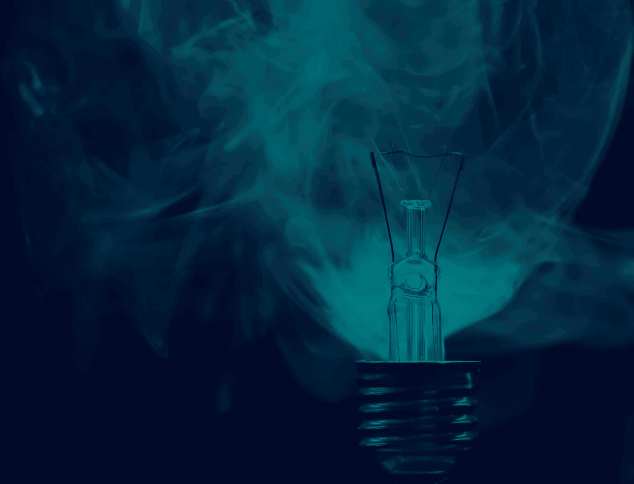